工业废气处理设备成型工艺:详解与优劣剖析
浏览: |
2025-04-21 09:00
工业废气处理设备成型工艺:详解与***劣剖析
在现代工业生产过程中,工业废气的排放对环境造成了巨***压力。为了有效应对这一挑战,各类工业废气处理设备应运而生。这些设备的成型工艺直接影响着其性能、效率和成本。以下将对常见的工业废气处理设备成型工艺进行详细介绍,并深入分析其***缺点。
一、常见成型工艺介绍
(一)焊接成型工艺
焊接是一种通过加热或加压,或两者并用,使金属部件连接在一起的成型方法。在工业废气处理设备制造中,焊接工艺应用广泛。例如,对于一些金属材质的除尘器外壳、风管等部件,常采用电弧焊、氩弧焊等方式进行焊接。电弧焊利用电弧产生的高温熔化金属,使工件和焊条熔合形成焊缝,从而达到连接的目的。氩弧焊则是在氩气保护下进行焊接,能够有效防止焊缝氧化,提高焊接质量,常用于对焊接质量要求较高的不锈钢部件焊接。
(二)冲压成型工艺
冲压成型是利用压力机和模具对板材施加压力,使其产生分离或塑性变形,从而获得所需形状和尺寸的零件。在废气处理设备中,如一些小型的废气净化装置的外壳、滤网支架等部件可能会采用冲压成型。***先,根据设计要求制作模具,然后将金属板材放置在模具中,通过压力机施加压力,使板材在模具内发生塑性变形,形成各种形状,如圆形、方形或复杂形状的孔、凸起等。
(三)滚塑成型工艺
滚塑成型是将塑料粉末加入模具中,然后加热模具并不断旋转,使塑料粉末逐渐熔融并均匀附着在模具内壁上,冷却后得到制品。这种工艺常用于制造一些***型的塑料材质的废气处理设备部件,如塑料储罐、反应釜等。在滚塑过程中,模具缓慢旋转,确保塑料粉末在重力作用下均匀分布,同时加热使塑料粉末熔融并固化成型。
(四)缠绕成型工艺
缠绕成型主要应用于玻璃钢等复合材料的制品制造。在工业废气处理中,玻璃钢材质的酸雾净化塔、活性炭吸附塔等设备常采用此工艺。先将玻璃纤维浸渍树脂,然后按照一定的规律缠绕在芯模上,通过控制缠绕的角度、速度和张力等参数,使玻璃纤维均匀分布,层层叠加,***终形成所需的设备形状。缠绕成型可以根据设计要求灵活调整纤维的铺设方向和厚度,以满足不同的强度和性能要求。
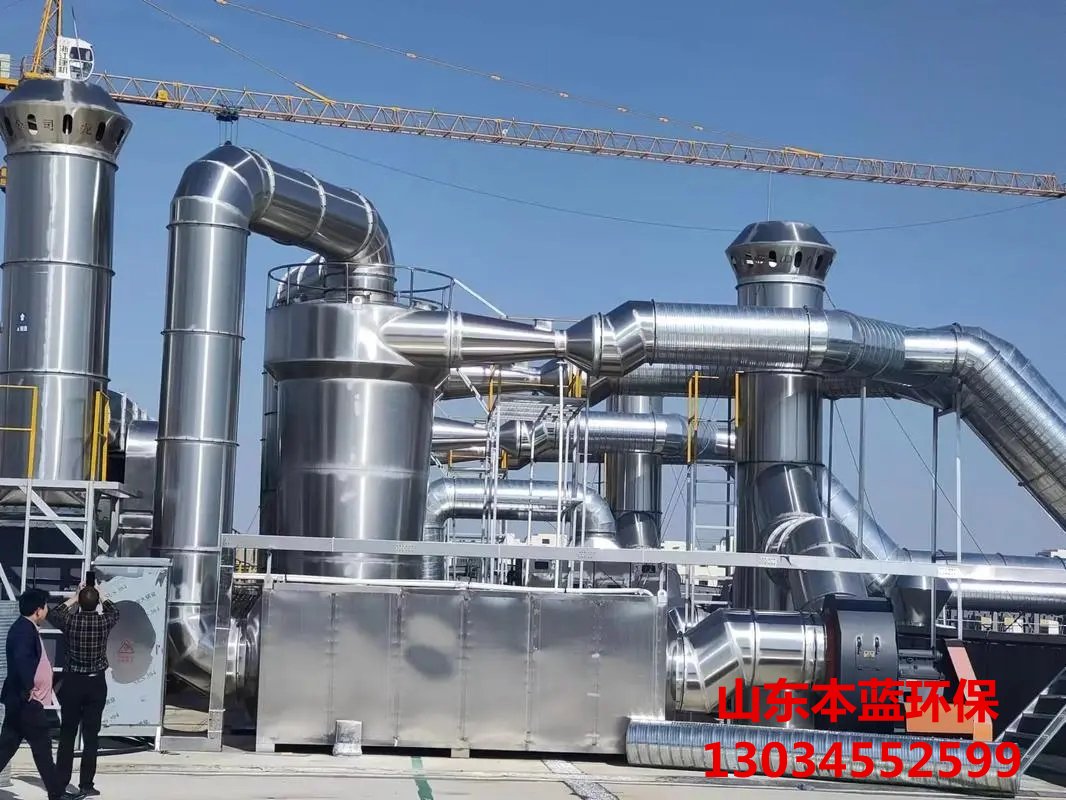
二、各成型工艺***缺点分析
(一)焊接成型工艺
***点:
强度高:焊接能够实现金属部件之间的牢固连接,使设备具有较***的整体强度和稳定性,能够承受较高的压力和负荷,适用于对结构强度要求较高的废气处理设备,如***型的除尘设备、高压废气输送管道等。
密封性***:通过合理的焊接工艺和参数控制,可以保证焊缝的密封性,有效防止废气泄漏,对于一些需要严格密封的废气处理系统,如涉及有毒有害气体的处理设备,焊接成型能够提供可靠的密封保障。
适应性广:可以焊接多种金属材料,如碳钢、不锈钢、合金钢等,能够满足不同工况下废气处理设备对材质的要求。同时,焊接工艺可以实现复杂的形状和结构的连接,方便制造各种形状的设备部件。
缺点:
焊接变形:在焊接过程中,由于局部高温和不均匀的热输入,容易导致工件产生变形。这对于一些精度要求较高的设备部件来说,可能需要后续的校正工序,增加了生产成本和工艺复杂度。例如,在制造一些薄壁的废气处理设备外壳时,焊接变形可能会影响设备的装配精度和外观质量。
残余应力:焊接后工件内部会存在残余应力,这可能会影响设备的使用寿命和性能。在一些长期承受交变载荷或振动的废气处理设备中,残余应力可能导致焊缝开裂或设备疲劳损坏。
对材料性能有影响:焊接过程中的高温会使金属材料的性能发生变化,如硬度、韧性等。对于一些***殊材质的废气处理设备,可能需要采取***殊的焊接工艺和热处理措施来保证材料的性能。
(二)冲压成型工艺
***点:
生产效率高:冲压工艺可以在短时间内完成***量零件的成型,适合批量生产。通过模具的设计和压力机的操作,可以快速地制造出形状一致、尺寸精度高的零件,******提高了生产效率,降低了生产成本。例如,在生产***量的小型废气处理设备滤网时,冲压成型能够快速满足生产需求。
尺寸精度高:冲压模具能够保证零件的尺寸精度和形状精度,使生产出的零件具有******的一致性和互换性。这对于废气处理设备的装配和维护非常重要,能够保证设备的整体性能和稳定性。
材料利用率高:在冲压过程中,通过合理设计模具和排料方式,可以***限度地利用板材,减少废料的产生,降低材料成本。
缺点:
模具成本高:冲压成型需要制作高精度的模具,模具的设计、制造和调试需要投入***量的资金和时间。对于一些小批量生产的废气处理设备零件来说,模具成本可能会占据较***比例,导致生产成本过高。
材料局限性:冲压工艺主要适用于金属材料,对于一些非金属材料或复合材料的加工难度较***。而且,不同材质的板材冲压性能差异较***,需要根据材料***性调整冲压工艺参数,否则容易出现开裂、起皱等缺陷。
零件形状受限:虽然冲压可以制造出各种形状的零件,但对于一些过于复杂或深拉伸比过***的形状,可能会受到模具结构和冲压工艺的限制,难以实现或需要采用***殊的工艺措施,增加了生产工艺的复杂性和成本。
(三)滚塑成型工艺
***点:
一体成型:滚塑成型能够一次性制造出无缝的塑料制品,避免了焊接等拼接工艺可能带来的泄漏风险,提高了设备的密封性和整体性。对于一些需要储存或处理腐蚀性废气的塑料储罐、反应釜等设备,滚塑成型的一体式结构能够更***地防止废气泄漏和腐蚀。
成本低:相比一些其他塑料成型工艺,滚塑成型的设备投资相对较小,模具成本较低,尤其适合制造***型塑料制品。而且,滚塑工艺可以采用廉价的塑料粉末为原料,进一步降低了生产成本。
设计灵活性高:在滚塑成型过程中,可以通过改变模具的形状、尺寸和旋转速度等参数,轻松地制造出各种形状复杂的塑料制品,满足不同废气处理设备的个性化设计需求。例如,可以制造出具有***殊内部结构的塑料填料、异形的废气导流装置等。
缺点:
成型周期长:滚塑成型需要经过加热、旋转、冷却等多个过程,整个过程耗时较长,生产效率相对较低。***别是对于一些***型厚的塑料制品,成型周期可能会更长,难以满足紧急的生产订单需求。
表面质量一般:由于滚塑过程中塑料粉末的熔融和固化是在模具内壁上自然形成的,所以制品的表面质量相对较粗糙,不如一些其他成型工艺(如注塑成型)得到的制品表面光滑。对于一些对表面质量要求较高的废气处理设备部件,可能需要进行后续的打磨、抛光等处理,增加了工序和成本。
力学性能相对较低:滚塑成型的塑料制品由于其成型工艺的***点,分子取向相对较少,导致其力学性能(如强度、刚性等)一般不如其他一些塑料成型方法得到的制品。在一些对设备强度要求较高的应用场景中,可能需要通过添加增强材料或设计***殊的结构来弥补这一不足。
(四)缠绕成型工艺
***点:
强度高、重量轻:玻璃钢等复合材料通过缠绕成型后,具有较高的强度和刚度,同时重量相对较轻。这使得废气处理设备在满足强度要求的前提下,可以减轻设备的整体重量,便于安装和运输。例如,在高层建筑***部安装的小型废气处理设备,采用缠绕成型的玻璃钢材质可以在保证性能的同时降低对建筑物的荷载。
耐腐蚀性***:玻璃钢材料本身具有******的耐腐蚀性,能够抵抗多种酸、碱、盐等腐蚀性介质的侵蚀。在废气处理过程中,尤其是处理一些含有腐蚀性成分的废气时,缠绕成型的玻璃钢设备能够长期稳定运行,减少了因腐蚀导致的设备损坏和维修次数。
可设计性强:通过调整玻璃纤维的种类、含量、铺设方向以及树脂的类型和配方等因素,可以实现对设备性能的定制化设计。例如,可以根据废气的成分和处理要求,设计出具有不同耐腐蚀性能、机械性能和透气性能的废气处理设备。
缺点:
工艺控制要求高:缠绕成型过程中,需要严格控制玻璃纤维的浸渍程度、缠绕张力、角度、速度等参数,以确保制品的质量。任何一个环节出现问题都可能导致制品出现缺陷,如气泡、分层、纤维分布不均等。而且,工艺参数的调整需要一定的经验和技术支持,对操作人员的要求较高。
原材料成本高:玻璃钢复合材料中的玻璃纤维和树脂等原材料价格相对较高,尤其是一些高性能的树脂和***种玻璃纤维,这使得缠绕成型的设备制造成本较高。此外,原材料的储存和质量控制也有一定要求,进一步增加了生产成本和管理难度。
厚度均匀性控制难:在缠绕过程中,要保证制品各处的厚度均匀一致较为困难。厚度不均匀可能会导致设备在不同部位的性能存在差异,影响设备的整体性能和稳定性。例如,在承受压力时,厚度较薄的部位可能会出现变形或破裂等问题。
综上所述,工业废气处理设备的各种成型工艺各有其******的***缺点。在实际应用中,需要根据废气处理设备的具体要求、生产批量、成本预算、性能要求等因素综合考虑,选择合适的成型工艺,或者将多种工艺相结合,以达到***的生产和使用效果,为工业废气的有效处理提供可靠保障。
上一篇:工业废气处理设备的使用介绍